BLOG
Introducing Mitsubishi MR-J5 Servo Drive
October 20, 2020
-
RSI has integrated Mitsubishi MR-J5 drive with RMP EtherCAT motion controller. This is a very powerful drive with many advanced features.
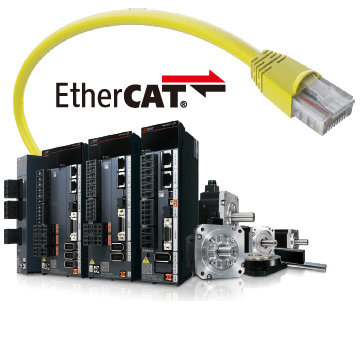
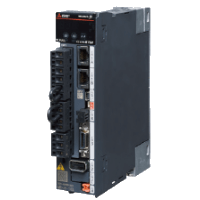
Tuning Functions
Use the tuning methods that are optimal for your machines
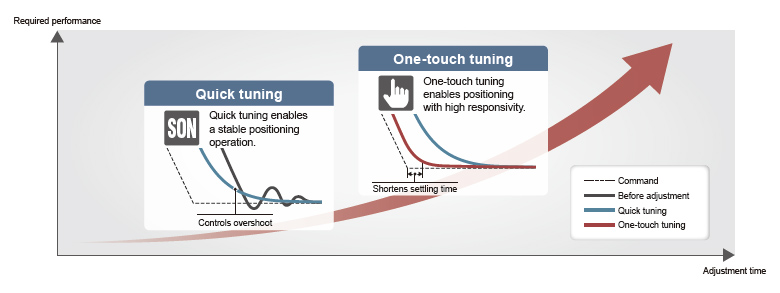
Quick Tuning
This function automatically performs easy-to-use auto tuning that controls vibration and overshoot just by turning on the servo-on command. Before normal operation, the servo amplifier sets control gain and machine resonance suppression filters in 0.3 seconds by inputting torque to the servo motor automatically. After completing the setting, the servo amplifier starts operation normally.
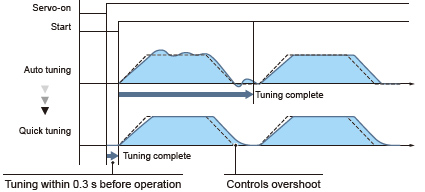
One-Touch Tuning
This function automatically completes servo gain adjustment according to the mechanical characteristics and reduces the settling time just by turning on the one-touch tuning. The servo gain adjustment includes the machine resonance suppression filter, advanced vibration suppression control II, and the robust filter. Controlling overshoot and vibration is improved, maximizing your machine performance.
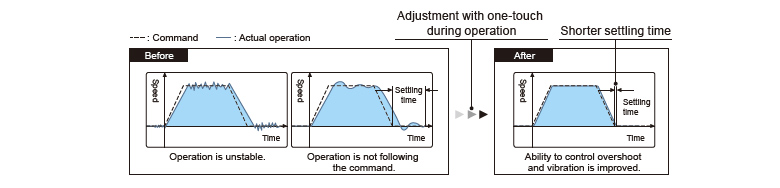
Advanced Vibration Suppression Control II
This function suppresses two types of low frequency vibrations, owing to vibration suppression algorithm which supports three-inertia system. This function is effective in suppressing residual vibration with relatively low frequency of approximately 100 Hz or less generated at the end of an arm and in a machine, enabling a shorter settling time. Adjustment is easily performed on MR Configurator2.
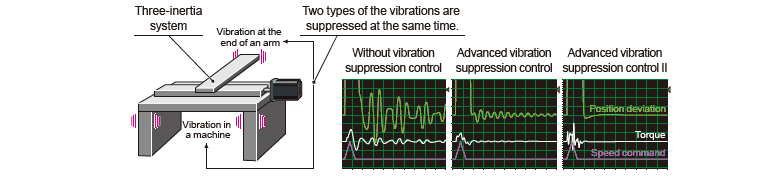
Command Notch Filter
The frequency can be set close to the machine vibration frequency because the command notch filter has an applicable frequency range between approximately 1 Hz and 2000 Hz.
Machine Resonance Suppression Filter
The expanded applicable frequency range is between 10 Hz and 8000 Hz. Five filters are simultaneously applicable, improving vibration suppression performance of a machine. The machine resonance frequency is detected by the machine analyzer function in MR Configurator2.
Reduced Energy & Max Space with Wiring
Utilizing a common bus connection conserves energy through the efficient use of regenerative power. Wiring can be simplified and installation space can be saved by reducing the number of molded-case circuit breakers and magnetic contactors. The MR-CM simple converter can connect to up to six compatible servo amplifiers having a total capacity of 3 kW or lower.
Wiring for the bus and the control power supply can be simplified by using daisy chain power connectors for passing wiring.
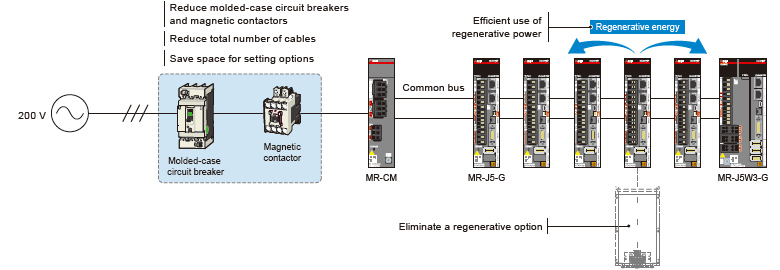
Machine Diagnosis (Ball Screws/Linear Guides)
This function supports predictive maintenance by estimating frictions and vibrations of mechanical drive components such as ball screws and linear guides.
- Friction failure prediction with the friction estimation function
- Vibration failure prediction with the vibration estimation function
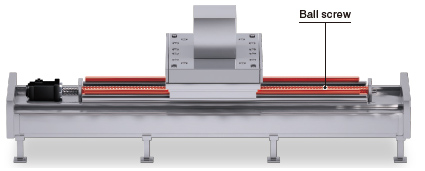
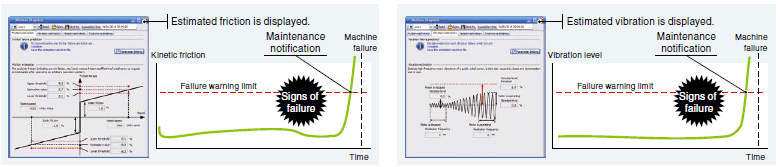
Machine Diagnosis (Belts)
This function detects aging deterioration of belts in advance by the static friction failure prediction and the tension deterioration prediction with the belt tension estimation.
- Static friction failure prediction
- Belt tension deterioration prediction
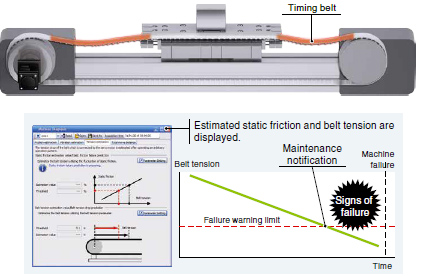
Machine Diagnosis (Gears)
With this function, the servo amplifier generates commands automatically, and executes to-and-fro positioning operation to estimate the amount of gear backlash. Gear failure is predicted based on the set nominal values for backlash.
- Backlash estimation function
- Gear failure prediction
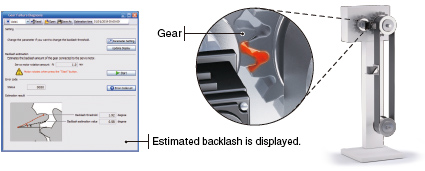
Safety Sub-Functions Compliant with IEC/EN 61800-5-2
MR-J5-G-RJ supports safety sub-functions, STO/SS1/SS2/SOS/SBC/SLS/SSM/SDI/SLI/SLT.
Refer to “Safety Sub-Functions” in section 1 of this catalog for the safety sub-functions and the safety levels, which vary depending on the combinations of the servo amplifiers and the rotary servo motors (including servo motors with functional safety)/linear servo motors/direct drive motors.
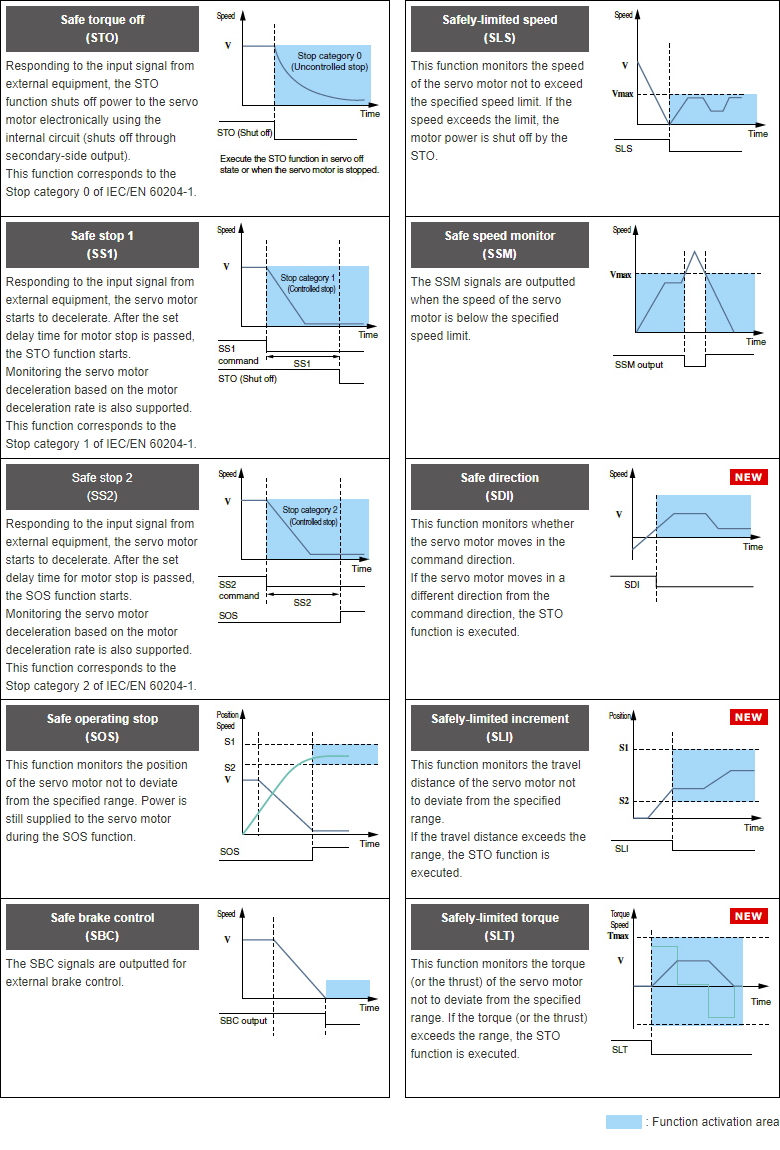
Touch Probe Function
MR-J5-G-RJ/MR-J5W2-G/MR-J5W3-G servo amplifiers can latch a position feedback value when the probe detects a target. The latched position feedback value read by the controller can be used for measurements and alignment. The touch probe supports the latch accuracy of 1 μs.
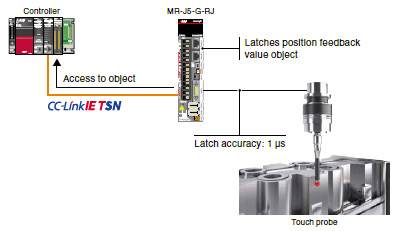
EtherCAT
EtherCAT
®
-compatible servo amplifiers are available, enabling higher-performance MR-J5 servo amplifiers with enhanced functions on the EtherCAT
®
system. MR-J5-G-RJN1/MR-J5W2-G-N1/MR-J5W3-G-N1 support the touch probe. (Latch accuracy: 1 μs )
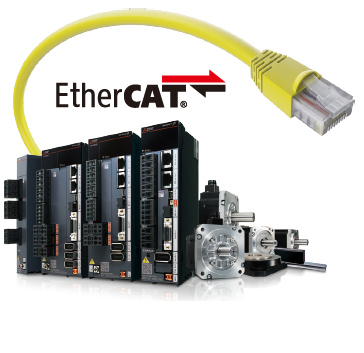
On this page
start developing today!
1000+ customers have already automated with help of our products and team