Case Study
Coil Winding Machine
- Reached production ahead of schedule utilizing the RMP motion controller, intuitive API, and diagnostic utilities.
- Several RMP features enabled synchronized and coordinated motion between multiple axes.
- Motion control hardware was selected to exceed machine performance goals.
- Single point of contact for support from development through production.
- Motion system was delivered under budget.
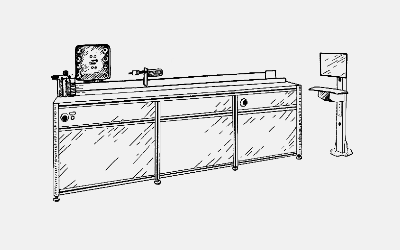
Solution
Motion Controller Features
Using the RMP EtherCAT Motion Controller to Build a Coil Winding Machine
The RMP EtherCAT Motion Controller includes multiple features which enable coil winding machine builders to synchronize motion between axes, seamlessly transition between recipe segments and synchronize filament wire tension within a recipe. Some notable controller features are outline below:
Multi Axis Streaming Motion is a type of synchronized motion where the machine builder will create an array of position and time points representing a motion profile for multiple axes. This method is a better choice for the execution of coil recipes because it allows the user to create a predefined multiaxis array of positions and times for each axis. The controller then executes the array synchronously so that each axis is coordinated and the transitions between relationships are extremely precise and repeatable.
RapidSequencer is a feature of the RMP motion controller that can run a user-defined algorithm in real-time. This feature allows the machine builder to create a custom control loop to evaluate a dancer or load cell feedback and output a torque setpoint to the unwind motor in order to tightly control the filament wire tension. The loop executes as a background RTOS task and it is very deterministic. This feature enables the best tension control performance.
Streaming Motion Sync Outputs is an RMP feature that allows the machine builder to synchronize filament tension force within the PT part profile motion array. Multiple segments within the array could have different filament wire tension setpoints. This feature allows the transitions between setpoints to be precisely coordinated with the part profile PT motion array.
Electronic Gearing is a feature that links two or more axes such that the position of the “slave” axis is a function of the position of the “master” axis. It would be useful to electronically gear the chuck motors 1 and 2 as their relationship will always be a perfect one to negative one relationship. Electronic gearing would be well suited to operate the chuck motors in manual or jogging mode.
Real-Time Triggers is a feature that can compare two inputs and trigger an interrupt or action within the RTOS. This feature could be used as an alternative method to streaming motion to execute coil recipes. The transitions between segments would be smooth and repeatable because transition events would be executed in real-time based on the position of the linear slider.
Testimonial
Technologies
Benefits
- Customer uses multiple EtherCAT vendors based on axes requirements and machine type.
- Unlimited system support for development, commissioning, and field machines.
- Motion solution delivers in performance, reliability, and price.
Images
Additional
Applications
Precision coils are used in many medical applications such as guidewires, catheters for endovascular, neurovascular, and cardiovascular surgeries. They are also used to make stent delivery systems. Coils can also be used in many industrial applications such as borescopes for visual inspection and several applications for the automobile and aerospace industries.
Axes of Motion
Coil Winding Machines have a variety of Axes:
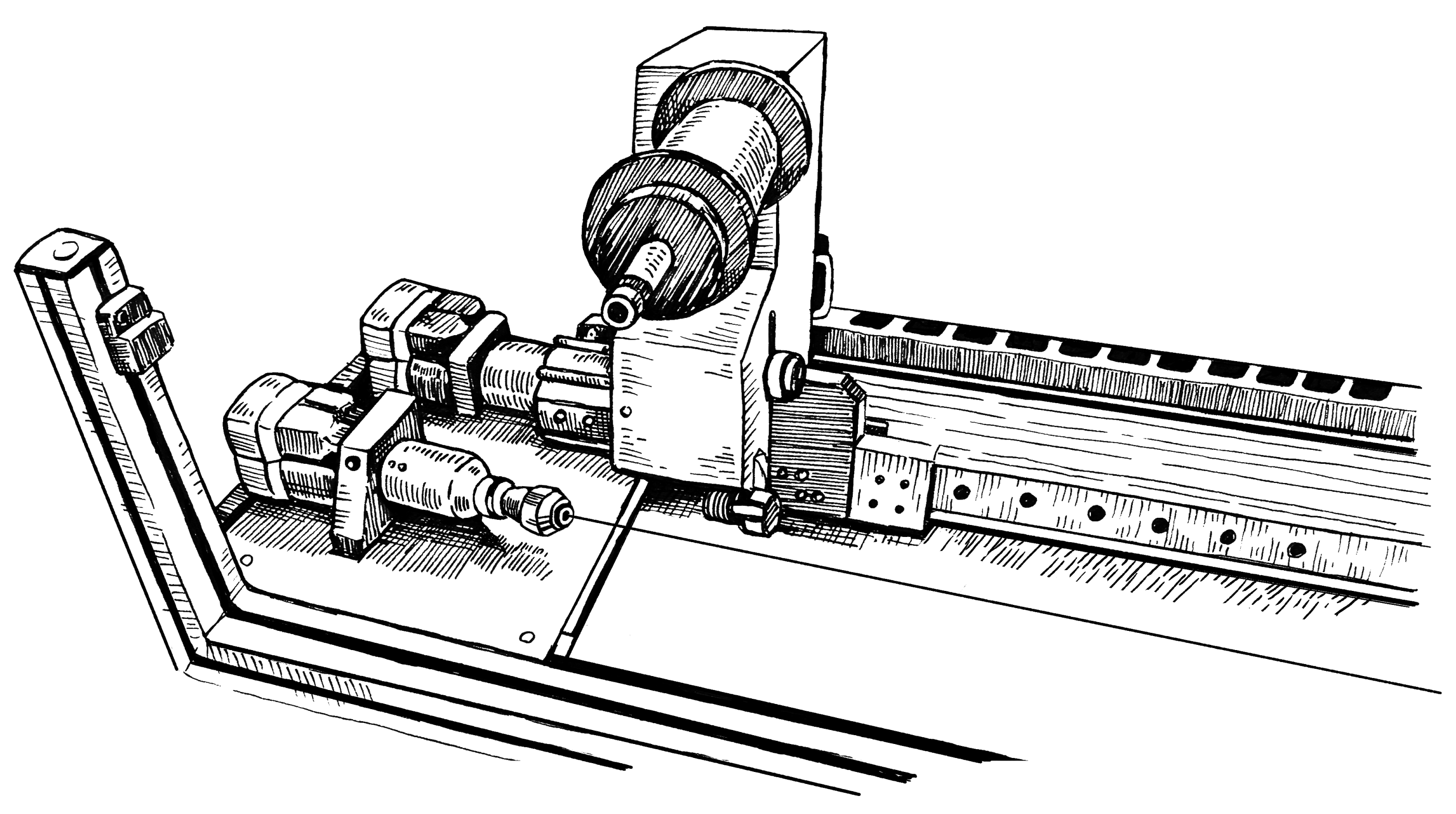
Chuck Motors – controls the rotational speed of the spinning mandrel coil support.
Linear Slide – controls the feed position of the filament wire which gets wrapped around the spinning mandrel.
Filament Wire Unwind Motor – controls the filament wire tension as it is wrapped around the mandrel.
Tailstock Slider – adjusts the position of the tailstock to allow for different length mandrels and coils.
Auxiliary Axes – several axes can be added to perform various automatic functions depending on machine features such as automatic cutting/feeding wire, automatic chuck tightening/loosening, automatic mandrel support guides, and automatic coil unload.
Fun Fact
Precision coiling machines are capable of handling a variety of filament wire materials and sizes. Filament wires can be as small as 0.0006” with coil diameters down to 0.007” which is comparable to the diameter of a human hair. Advanced motion control systems are required to achieve such precision.
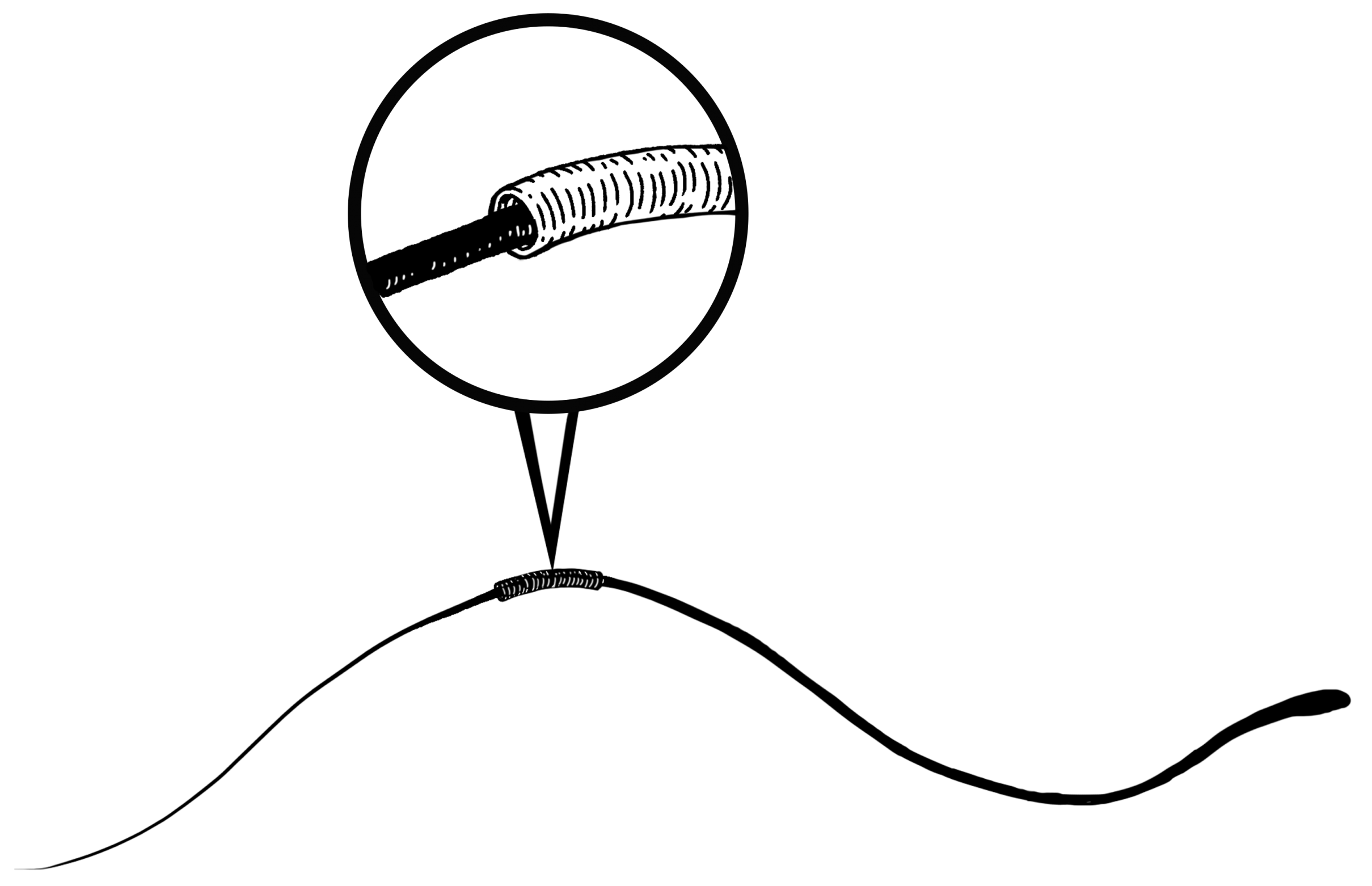
Process Variables
Coil Winding Machine Terms & Definitions:
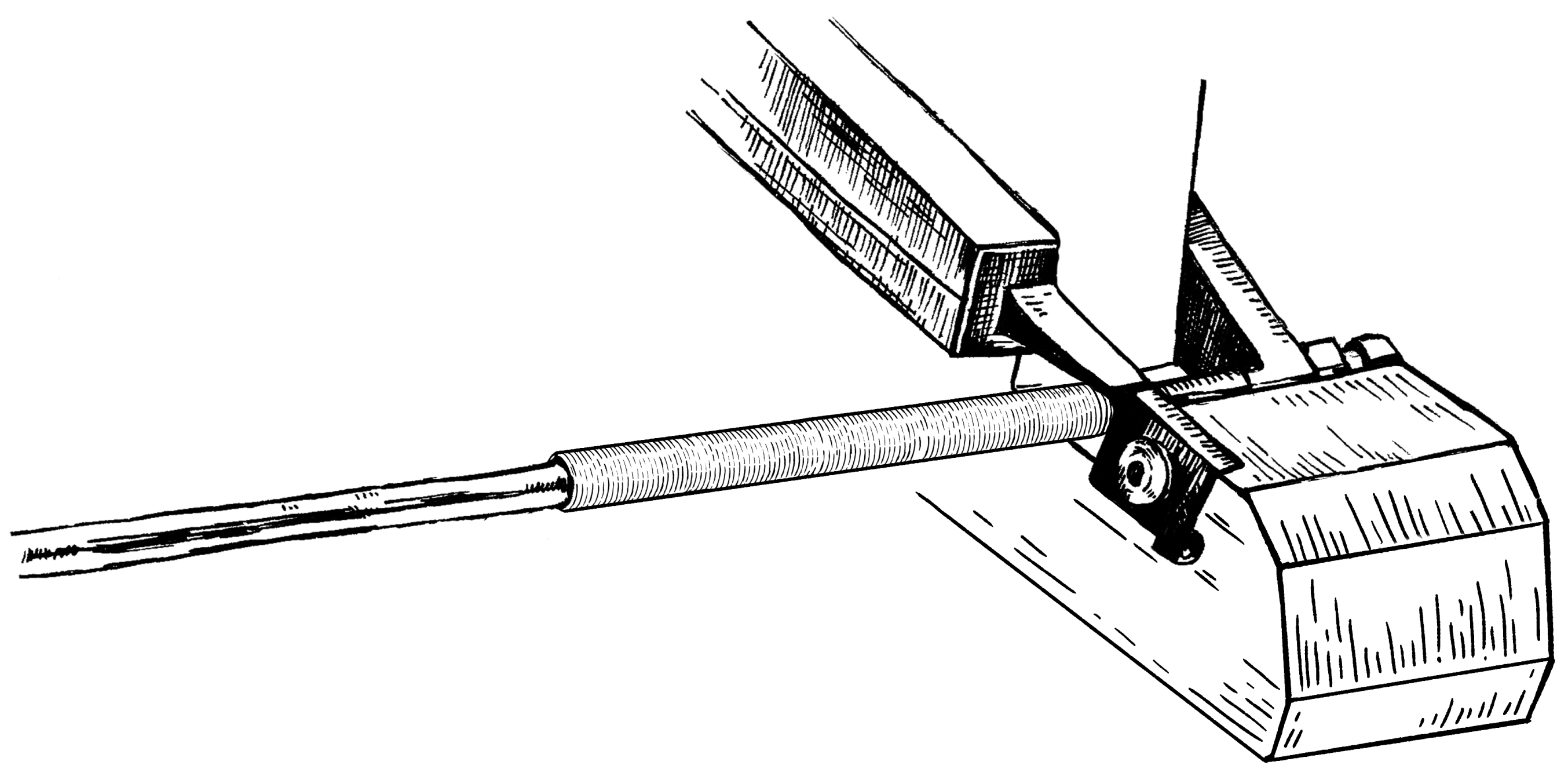
Coil Pitch: the distance between center of the coil thread to the adjacent coil thread. It is controlled by the relationship of the chuck motors and linear slider speeds. The speed relationship must account for the desired coil pitch, filament wire diameter, and mandrel diameter. The pitch can vary multiple times for a single coil depending on the design. The pitch is usually given in units of revs per inch. The pitch tolerances on some coils could be 0.0002” or less depending on the coil design.
Mandrel Speed: the rotational speed of the mandrel while winding the coil. The higher the mandrel speed, the faster it wraps the coil resulting in higher machine throughput.
Filament Wire Tension: created by the filament wire spool unwind motor providing a resistance pull on the wire as it is wound on the mandrel. A tension control loop is required to use feedback from dancers, and or load cells to maintain the desired tension setpoint. The tension must be tightly controlled even though the speed at which it gets unwound varies based on filament wire spool diameter, mandrel speed, and coil pitch. It is critical to ensure desired tension is applied at all times. The desired tension may also vary multiple times for a single coil depending on the design.
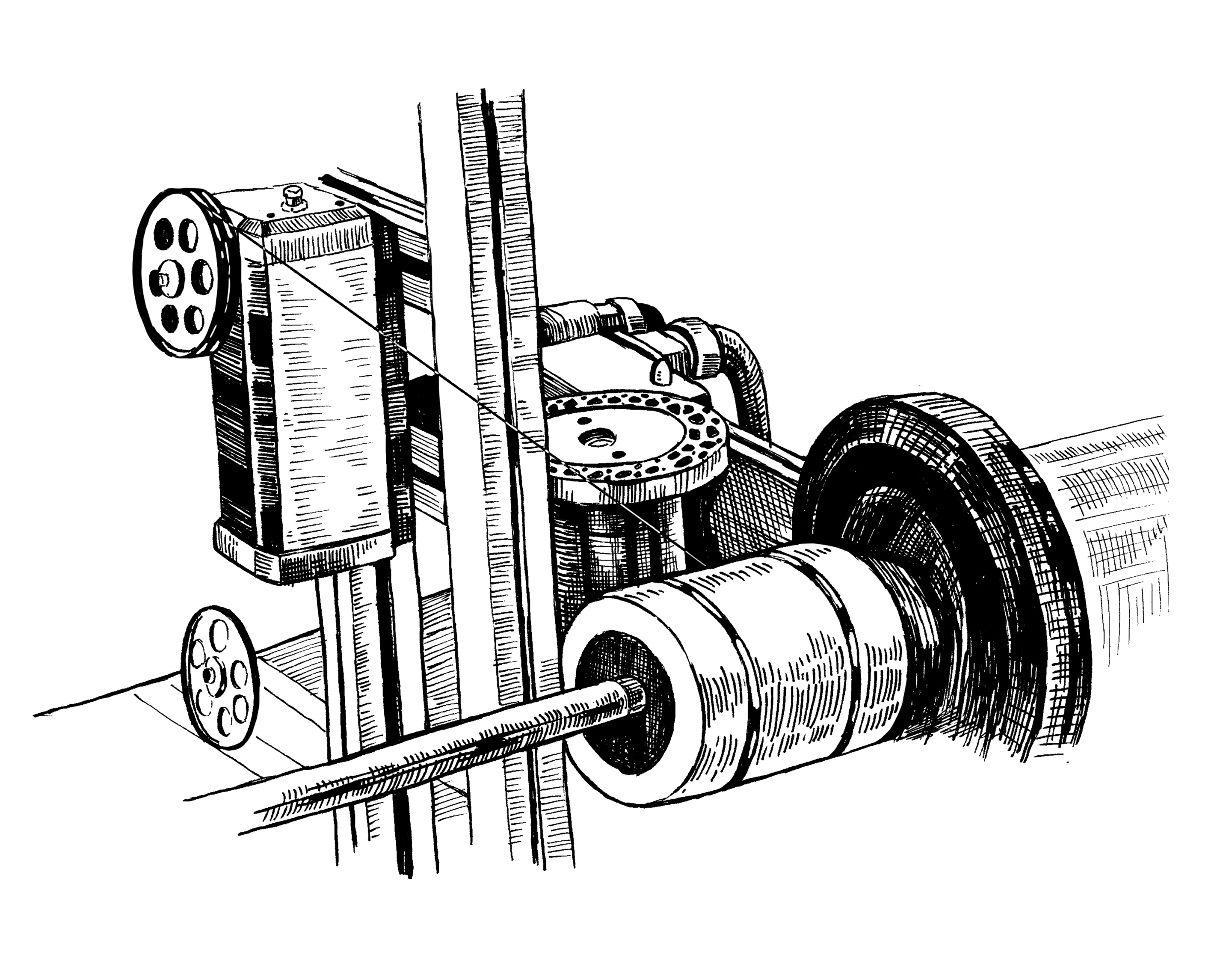
Coil Length: the desired length of the coil and is determined by the travel distance of the linear slider. For longer coil lengths, the tailstock can be adjusted to accommodate longer support mandrels.
Coil Diameter: the desired diameter of the coil and is determined by the spinning support mandrel diameter. It is possible to vary the coil diameter throughout the length of the coil.
Coil Recipes: created to define an entire coil design using all of the above parameters . The recipe may contain multiple segments where the pitch, tension, diameter or speed varies for a given length of segment. The machine must seamlessly transition from segment to segment until the recipe is complete. Once the recipe parameters for each segment are finalized, it can be executed by the motion controller to produce consistent and repeatable coils.
On this page